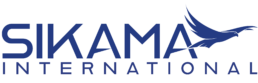
Before entering the heating zones, the substrate temperature is stabilized in a liquid-cooled load zone. Each heat zone has individual temperature set point and gas flow controls that maintain platen temperature to within +/- 1% to ensure reliable, repeatable profiles. The cover gas is introduced into the reflow chamber through micro-perforations in the bottom heating platens and enters the chamber at the same temperature set for each zone. The last internal liquid-cooled zone ensures a process cool-down in an inert atmosphere. Additional cooling of the substrate is accomplished as the product exits into the liquid-cooled offload zone.
Components are transported through the furnace by sweeper bars that can operate continuously or in a “dwell” (timed delay) mode which is a unique feature offered only by Sikama and which produces superior temperature uniformity in the reflow profile while utilizing the smallest footprint in the industry. The Falcon 1200 can be interfaced with a computer for storing profiles, monitoring individual heat zone temperatures as well as speed and time controls including remote operation.
The Falcon 1200’s minimal use of electricity and gas is the result of Sikama’s unique design for balanced heating and cooling that will ensure the highest performance at the lowest cost.
Fill out the form below to download Sikama International's Datasheets
You have successfully joined our subscriber list.
May be added at any time – furnish serial number.
Part# | Description |
2701 | Software Package (Windows 7/10) |
9648 | Uninterruptible Power Supply, 220V |
Kit | Zero Down Time Kit (2 Years Minimum Support) |
System Serial Number must accompany spare parts order.
Part# | Description |
1095 | Flow Switch – Water/Gas |
2198 | Contactor, Main Power |
2200 | Heat Zone Assembly |
2225 | Equipment Manual, Falcon 1200 |
Sikama International’s Falcon 1200 is a budget-friendly furnace capable of temperatures up to 400°C that can be used across a broad range of substrate materials including wafer bump reflow, insulated metal-core substrates, BGA, high mass components, and epoxy curing applications including underfill and glob-top. Incorporating Sikama’s unique conduction heating in combination with forced thermal convection and radiant heating, the Falcon 1200’s 1 load zone, 7 heat zones, and 2 cooling zones provide precise profiling capabilities. The automatic load and unload buffers with SMEMA interface allow easy integration into automated production lines. The heating chamber provides extremely low vibration and <10ppm O2 levels throughout the entire heating chamber, not just the reflow zone. This product is CE certified and meets SEMI safety and ergometric standards.